Juni 2023
Bei erfolgreichen Geräten wurde konzeptionell genau das richtig gemacht, was der Markt gefordert hatte. Und zugleich wurde die richtige Produkt-Architektur auf die richtige Art und Weise umgesetzt. Der Grundsatz „Das Richtige richtig machen“ ist auch gültig für die elektromagnetische Verträglichkeit (EMV) des Produktes. Es braucht hierfür neben qualifizierten Ingenieuren, die methodische Lösungen erarbeiten, auch eine entsprechende Messumgebung. Dabei ist die elektromagnetische Verträglichkeit auf Geräte-Ebene so komplex, dass nur spezielle Messungen aussagekräftige Resultate liefern. Für eine effiziente und agile Produktentwicklung hat Helbling beide Kompetenzen inhouse gebündelt. Damit ist Helbling in der Lage, für seine Kunden anhand ihrer Inputs die optimale Relation zwischen Kosten und Qualität zu erzielen. Dies gilt gleichermassen für das Produkt wie die Entwicklungstätigkeiten.
Eine Elektronik für ein Gerät zu entwickeln, ist in den letzten fünf Jahren vielschichtiger geworden. Ob es sich um Lifestyle- oder Medtech-Produkte handelt: Es gilt aktuell das Narrativ: „Sense and Simplicity“. Jedes Gerät soll einfach zu bedienen, zugleich aber auch „smart“ sein. Hierdurch haben jedoch zukünftige Gerätegenerationen para-doxerweise deutlich mehr sekundäre Funktionen erhalten. Anstelle von Knöpfen, Schaltern oder Hebeln sind nun Touch Displays, Apps, Bluetooth und KI gefordert. Zudem gibt es gesellschaftlich einen Konsens darüber, dass Geräte im Betrieb weniger Energie verbrauchen und ressourcenschonend produziert werden sollen.
Hieraus ergibt sich die Anforderung, die elektronischen Schaltungen an den Grenzen des technisch Sinnvollen und Machbaren zu optimieren. Aktuelle Schaltungsarchitekturen weisen in der Regel mindestens eines der folgenden Elemente auf:
- Mikroprozessor
- Kommunikationsmodul
- Display
- getaktete Schaltstufen und Leistungsstufen wie das Netzteil
Alle Elemente haben gemeinsam, dass diese mit einen Grundtakt geschaltet werden. Ein unerwünschter Nebeneffekt der getakteten Schaltungstopologie ist, dass es steile Flanken gibt, die elektromagnetische Störungen aussenden. Im Vergleich zu einer anlogen Topologie ist der Störpegel in der Regel höher. Das Kommunikationsmodul beinhaltet meist eine Antenne, die mit einem definierten Pegel elektromagische Signale abstrahlen soll.
Ein aktueller Trend ist es, die Spannungspegel immer weiter zu senken, um weniger Energie zu verbrauchen. Hierdurch werden die Schaltkreise aber auch störanfälliger und sensibler. Daher ist es wichtig, die eigene Störaussendung zu messen sowie die Stör-festigkeit der im Gerät verbauten Schaltungen gegenüber eingestrahlten Stör-spannungen zu prüfen.
Die Zusammenhänge bei der EMV sind in der Regel komplex. Deshalb ist ein ent-scheidender Erfolgsfaktor, die Komplexität auf ein beherrschbares Niveau herunter-zubrechen. Hierbei helfen Simulationen, theoretisches Grundwissen und Erfahrung, um bestimmte Phänomene besser verstehen und beeinflussen zu können. Eine Simulation ist nur so aussagekräftig wie das Modell, auf dem diese basiert. Komponenten und einfache Baugruppen lassen sich mit vertretbarem Aufwand exakt modellieren und simulieren. Auf Geräteebene hingegen sind Simulationen sehr aufwendig und bilden die Realität nur ungenau ab. Es gibt bisher keinen „Digital Twin“ eines Gerätes, der physikalisch die elektromagnetischen Eigenschaften des Originals hinreichend genau abbildet.
Einzig die Messung gibt verlässlich Aufschluss über die Geräterobustheit gegenüber Störungen und die Abstrahlungsintensität. Deshalb sollte die EMV ein integrativer Bestandteil der Produktentwicklung sein.
EMV-Testmöglichkeiten in der Entwicklungsumgebung bringen entscheidende Vorteile
Die spezielle, kostspielige EMV-Messumgebung und aufwendige sowie komplexe Messarbeit sind eine nicht zu unterschätzende Herausforderung. Insofern die Ressourcen intern nicht vorhanden sind, müssen häufig entwicklungsbegleitende Messungen in akkreditierten, kostenintensiven Messlaboren durchgeführt werden. Die Erfahrung zeigt jedoch, dass diese nicht auf das dynamische Umfeld der Produktentwicklung ausgerichtet sind.
Helbling bietet seinen Kunden eine heuristische Entwicklung mit interdisziplinären Teams. Die Infrastruktur bei Helbling ist den Bedürfnissen der Entwicklerteams an-gepasst. Diese können alle relevanten EMV-Tests für Geräte im Consumer-, Medical- und Industrie-Bereich vor Ort durchführen. Dabei handelt es sich um Pre-Compliance-Messungen, die jedoch zeitnah und schnell entwicklungsbegleitend durchgeführt werden. Am Ende einer Entwicklung wird die Verifikation der Normenkonformität formal durch ein akkreditiertes Messlabor bestätigt. Unter anderem kann so der Innovations-zyklus verkürzt werden.
Auf diese Weise wurden bereits zahlreiche Serienprodukte mit einer Jahresproduktion von 10k bis mehren Millionen Stück gemeinsam mit nationalen sowie internationalen Kunden auf den Markt gebracht. In der Regel wird nach dem Serienstart der ganze Produktlebenszyklus betreut. Helbling arbeitet dafür mit unterschiedlichen OEMs auf der ganzen Welt zusammen.
EMV-Infrastruktur@Helbling im Detail
Die EMV-Messungen lassen sich in die Bereiche „leitungsgebunden“ und „gestrahlt“ (durch die Luft) gliedern.
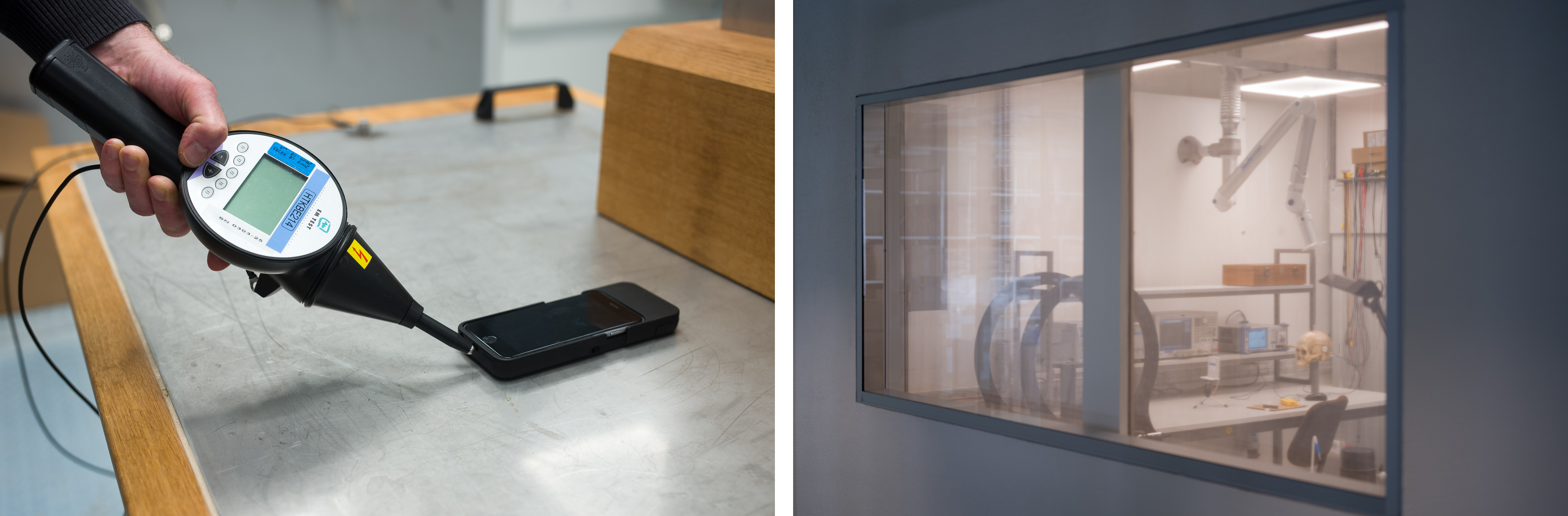
Bei leitungsgebundenen Messungen werden die Störpegel auf Leitungen und leitfähige Elemente der Maschine ein- beziehungsweise ausgekoppelt. Die Messung selbst wird in einem geschirmten Raum durchgeführt. Dieser spezielle Raum ist dringend notwendig, damit einerseits nur der Prüfling gemessen wird und nicht externe Störquellen. Anderseits soll die Umgebung bei der Störfestigkeitsprüfung nicht gestört werden.
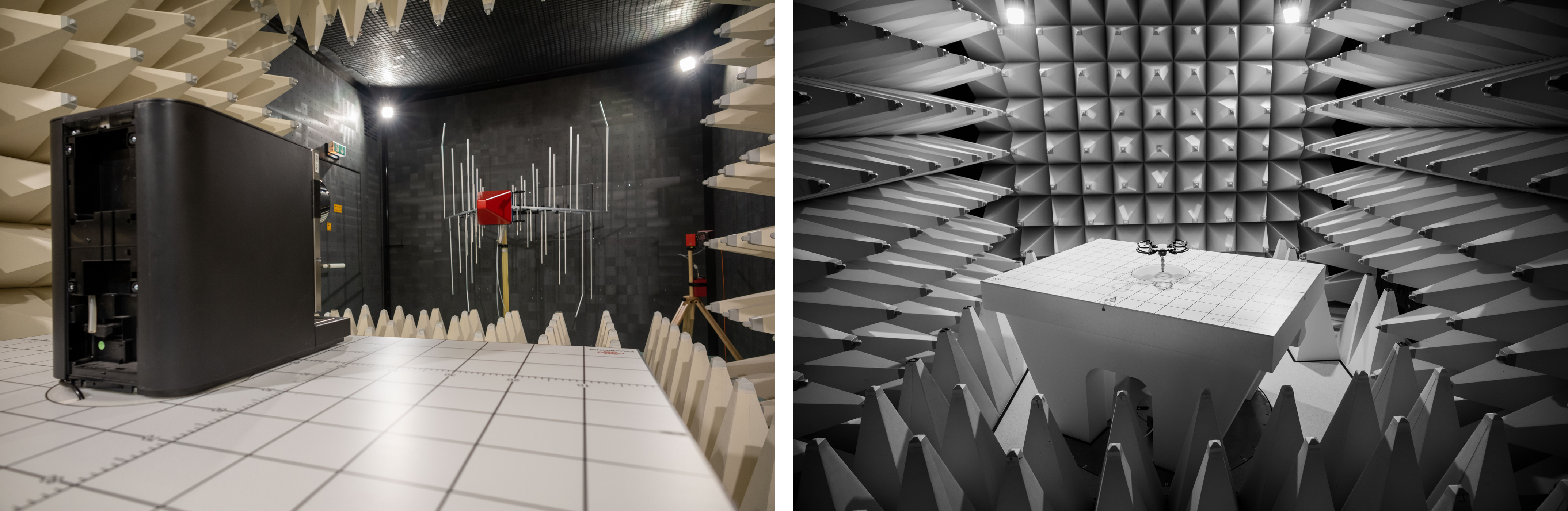
Bei gestrahlten Messungen werden Störungen untersucht, die durch die Luft übertragen werden. Es wird hierzu eine Absorberkammer benötigt. Eine Absorberkammer ist ein geschirmter Raum, der zusätzlich mit Ferrit-Platten und Absorber-Kegeln ausgestattet ist. Die Verkleidung der Oberflächen verhindert ein unkontrolliertes Ausbreiten der Wellen durch Reflektionen.
Fallbeispiel: EMV-Tests ermöglichen eine rasche Reaktion auf Lieferkettenprobleme
Helbling betreut zusammen mit Kunden das Product Life Cycle Management für verschiedene Geräte. Aufgrund der Lieferengpässe während der Corona Pandemie musste nach Lösungen und Alternativen für nicht mehr lieferbare Komponenten und Baugruppen gesucht werden.
Die besondere Herausforderung bestand darin, Produktionsausfälle zu vermeiden. Viele Elektronik-Komponenten waren ohne Ankündigung nicht mehr wie gewohnt verfügbar. Beim Evaluieren und der Freigabe von alternativen Komponenten musste sehr schnell gehandelt werden. Gerade für die Konsumgüter Branche ist es essenziell, schnell am Markt zu agieren. Eine Verlängerung der Lieferzeit reduziert meistens den Gewinn, da sich die Endkunden nach Alternativen umschauen.
Helbling konnte sich auf die neue Situation sofort einstellen und Lösungen anbieten, indem alternative Komponenten und Baugruppen umgehend auf Maschinenebene verifiziert wurden. Hierzu gehören auch EMV-Tests.
Im Fallbeispiel musste für einen professionellen Gerät zur Getränkezubereitung ein alternatives Display beschafft werden. Die Auswahl an Displays erscheint auf den ersten Blick gross, wird jedoch durch Vorgaben, wie Abmessungen, Auflösung, optischer Eindruck und Touch-Optionen reduziert. Die elektromagnetische Abstrahlung des Displays ist erfahrungsgemäss ein signifikanter Teil des Störpegels der Maschine und macht es somit zu einer kritischen Komponente.
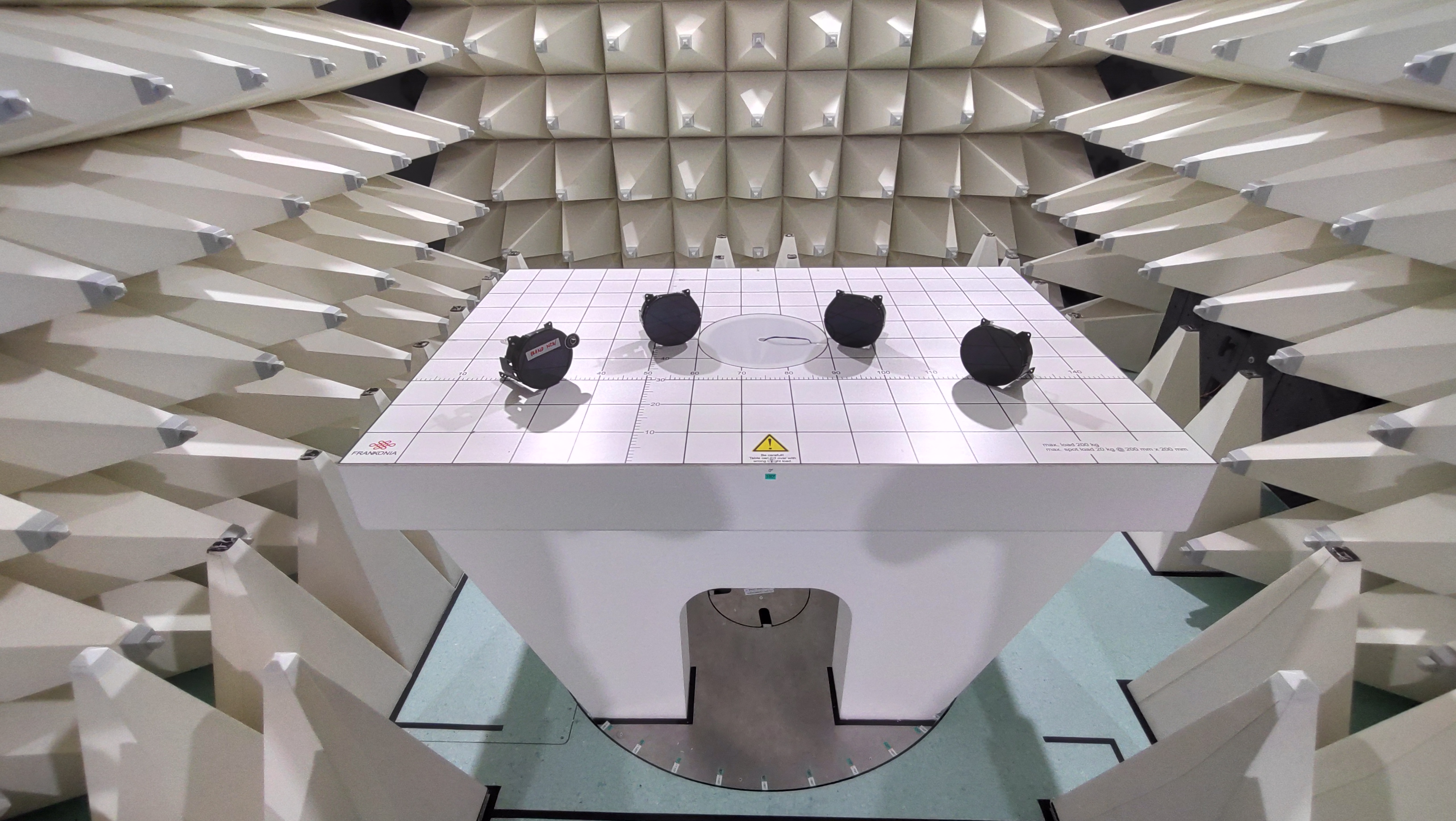
In dem weiter unten detailliert dargestellten Fallbeispiel wird erörtert, was der Wechsel einer Komponente für Auswirkungen hat. Der Störpegel, des alternativen Displays, war so hoch, dass eine entstörende Massnahme erarbeitet werden musste. Durch das methodische Vorgehen war es möglich, mit wenig Aufwand einen grossen Effekt zu erzielen und so den Pegel erheblich zu senken.
Zusammenfassung: Präzise EMV-Messungen vor Ort bringen Lösungen in kürzester Zeit
Eine Messumgebung für EMV-Tests ist matchentscheidend für die Produktentwicklung. Denn nur spezielle Messungen liefern aussagekräftige Resultate in Bezug auf die Geräterobustheit gegenüber Störungen und die Abstrahlungsintensität. Helblings Entwicklungsteams können inhouse für Projekte mit Kunden auf eine komplette EMV-Mess-Infrastruktur zurückgreifen. Dabei stehen ihnen ein abgeschirmter Raum für leitungsgebundene und eine Absorberkammer für gestrahlte Messungen zur Verfügung. Auf diese Weise werden neue Produktentwicklungen vorangetrieben und auch rasch Optimierungen im Rahmen des Lebenszyklus' eines Geräts durchgeführt.
Autor: Björn Sauer
Hauptbild: Helbling
Das Fallbeispiel im Detail
Beschreibung der Messung zum Displayersatz
Relevant für die gestrahlte elektromagnetische Verträglichkeit von Consumer-, Business-to-Business-, Medizinal- und Industrie-Geräten sind die Frequenzen von 30Mhz bis 1 GHz bzw. 6 Ghz. Die Messung der von der Maschine abgestrahlten elektromagnetischen Störungen findet in der Absorberkammer statt. Im Boden der Absorberkammer eingelassen, gibt es einen Drehteller, auf dem ein Tisch steht. Das Display wird auf einem Drehtisch ausgerichtet und in Betrieb genommen. Eine Antenne empfängt das Störsignal und ein Messempfänger wertet das empfangene Signal aus. Nachdem ein sogenanntes Frequenz-Sweep abgeschlossen ist, wird der Tisch gedreht und eine neue Messung gestartet. Auf diese Weise erfährt man, wie das Display rundherum, das heisst auf 360 Grad, abstrahlt.
Ausgangsgangsituation für das Fallbeispiel war, das kommerziell und aufgrund der technischen Daten drei Displays vorausgewählt wurden. Diese Displays wurden in der Absorberkammer ausgemessen. Auffällig war, dass alle drei Displays einen ausgeprägten Peak bei 300 MHz aufweisen. Dieser Ausschnitt ist in der nachstehenden Abbildung zu sehen. Display A und C haben einen höheren Peak als B, deshalb wurde auch B gewählt.
Verhalten des alternativen Displays in der Maschine
Die nächste Fragestellung war: „Wie verhält sich das Display im Maschinengehäuse?“ Das Display B wurde in die Maschine eingebaut und die Messung wiederholt. Abbildung 5 zeigt die Veränderung, wenn das Display in einer Maschine eingebaut ist. Der Peak bei 300 Mhz ist geringer geworden, aber bei 500 Mhz ist ein neuer Peak hinzugekommen, der zu nahe am Limit ist. Der 500-Mhz-Peak zeigt eindrücklich, wie sich das Abstrahl-verhalten einer Baugruppe im eingebauten Zustand ändern kann. Anhand der Einzel-messung der Displays war dieser Peak nicht vorhersehbar.
Für den Entwickler ist nun interessant zu verstehen, was bei 500 Mhz passiert ist. Hierzu wird eine andere Darstellung gewählt. In der Abbildung 6 ist die Feldstärke der einzelnen Positionsrichtung in Abhängigkeit zum Winkel dargestellt. Das linke Diagramm visualisiert die Messung des Displays als Einzelkomponente und das rechte die Messung mit eingebautem Display in die Maschine. Man erkennt, wie sich die Polarisation ver-ändert und das elektrische Feld in Richtung Maschine Front abstrahlt wird. Die Maschine wie auch ihr Gehäuse wirken als Reflektor für diese elektromagnetische Welle.
Durch diese Messung auf Maschinenebene wurde das Risiko erkannt, dass man nahe am Normativen Limit ist und es bei einer späteren externen Messung zu einer Nicht-Norm-Konformität kommen kann. Nach Rücksprache mit dem Kunden wurde beschlossen, das Display zu optimieren, um mehr Reserve zu haben.
Optimierung
Für die Optimierung wurden weitere Messungen mit dem in die Maschine eingebauten Display durchgeführt. Es wurden sukzessive die Funktionseinheiten des Displays eingeschaltet, um deren Störpegel zu ermittelt. In der Abbildung 7 erkennt man in Grün den Störpegel des Controllers. Zu diesem Pegel kommt in Gelb das Display und in Blau das Backlight hinzu. Rechts neben dem Peak ist grafisch der Betrag der einzelnen Störpegel dargestellt. Das Display selbst weist den grössten Pegel auf, gefolgt vom Controller. Das Backlight hat einen geringeren Anteil.
Schaltungstechnisch sind Display und Controller abgeschlossene Einheiten. Eine Modifikation dieser Einheiten ist sehr aufwendig. Die Schaltung des Backlights ist hingegen deutlich einfacher und die Schaltung hat noch nicht ausgeschöpftes Ver-besserungspotenzial. Deshalb folgte eine Analyse der Schaltung des Backlights und eine Erarbeitung möglicher Optimierungen (vgl. Abbildung 8). Durch eine kurze Simulation konnte selektiv ein Ferrit ausgewählt werden. Bei der Ferrit-Perle handelt es sich um ein sehr kleines und kostengünstiges Bauteil im einstelligen Euro-Cent-Bereich. Es wurde mit minimalem Mehraufwand viel Wirkung erzielt.
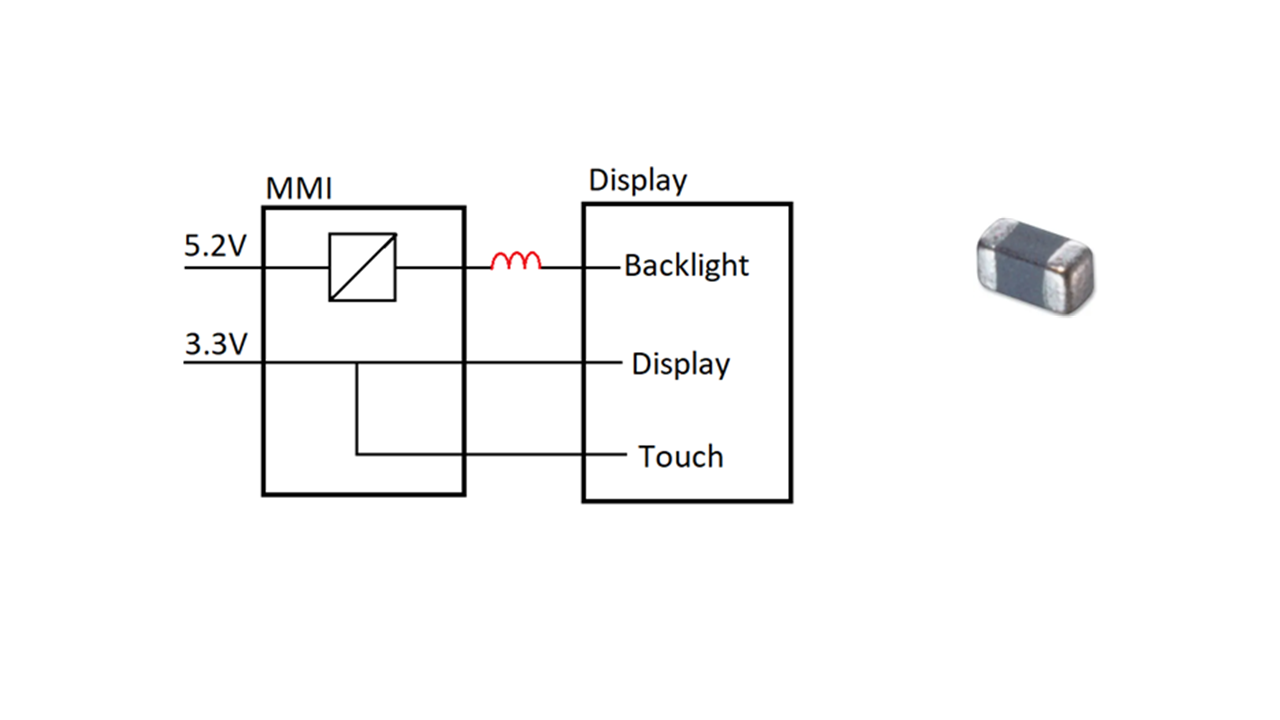
Abschliessend wurde als Verifikation noch eine Messung durchgeführt: Die hohen Peaks bei 300 MHz und 500 MHz konnten soweit gesenkt werden, dass genügend Reserve zum Limit vorhanden ist und kein Risko mehr besteht, bei einer normativen Zulassungs-messung in einem akkreditierten Messlabor nicht zu bestehen.