Technologies
November 2021
Robotics is experiencing a boom and mobile robotics is playing a key role in this. More and more applications are using the ability to move and orient oneself independently in a changing environment. This trend is currently evident in the rapidly growing online trade in logistics. But how can these complex applications be put into practice efficiently? Helbling uses a show case to demonstrate how autonomous navigation can be implemented with reasonable effort thanks to industrialized components.
Why mobile robotics?
It is called HelMoRo, comes from a 3D printer, and can autonomously find and manipulate objects. The “Helbling Mobile Robot” was developed in recent months by Helbling engineers using agile methods and is considered a showcase. Commercially available components and software modules are used for this platform. The experts use it to determine which robotics solutions are possible for complex contexts with justifiable effort and risk. There is a great need for this: Helbling develops sophisticated robotic systems for clients from a wide range of industries. An important element of this is mobile robotics, which has become increasingly important in many applications in recent years. Typical mobile robots are self-driving vehicles and drones.
The advantage of an autonomously navigating robot is that it can independently find its way and move around in a changing environment, free of fixed installations. This allows automation of tasks in difficult to access, dangerous, or changing environments, on land, at sea, in the air and even in space.
Autonomous navigation vehicles have become an indispensable part of logistics and automated manufacturing. The importance of autonomous navigation is increasing in the areas of mobility, inspection, and reconnaissance too. There, the mobile robot acts as a carrier of sensors and actuators, for example in agriculture, where mobile robots identify and selectively remove weeds, or as a means of transport for goods and people.
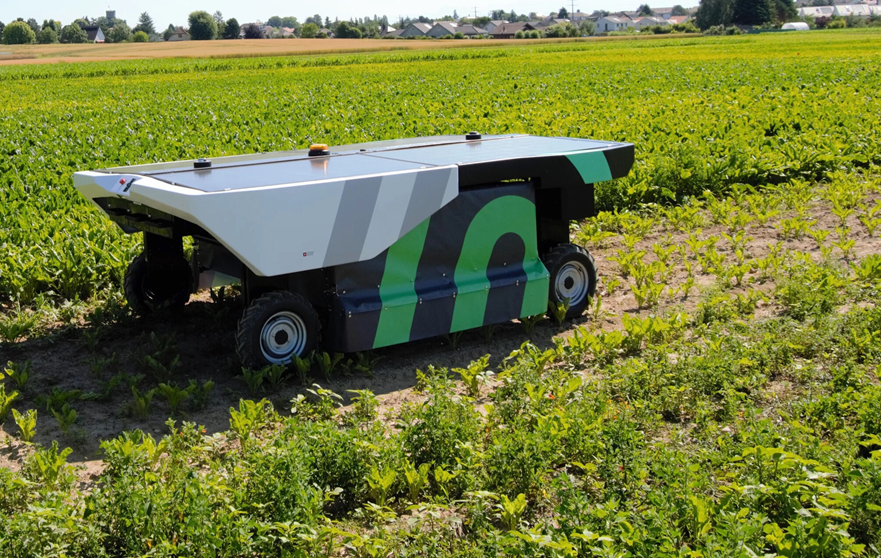
What makes up mobile robotics?
A core aspect of all these applications is autonomous orientation and navigation in an at least partially unknown and changing environment. More precisely, it is about recognizing the environment, building and tracking one’s own map, and finally navigating with it, including reacting to deviations from the map.
Implementation of these partial aspects differs depending on the application. In logistics, for example, an AGV (automated guided vehicle) usually moves on level ground, often in a well-described environment, but must react to obstacles and meet high personal safety requirements.
On the other hand, an inspection drone in an unknown, harsh environment needs to continuously capture the relevant aspects of the environment and augment a digital map with its own position in real time. This enables it to reliably determine the path to the target point and avoid collisions. This type of autonomous navigation is referred to as SLAM (simultaneous localization and mapping).
The different areas of application require a balanced range of sensors to detect the environment, such as laser-based sensors (LIDAR), two- or three-dimensional camera systems, as well as ultrasonic or capacitive sensors. Algorithms tailored to the application are used for this purpose. These enable the evaluation and fusion of sensor data for localization as well as dynamic planning of the path to the intended target.
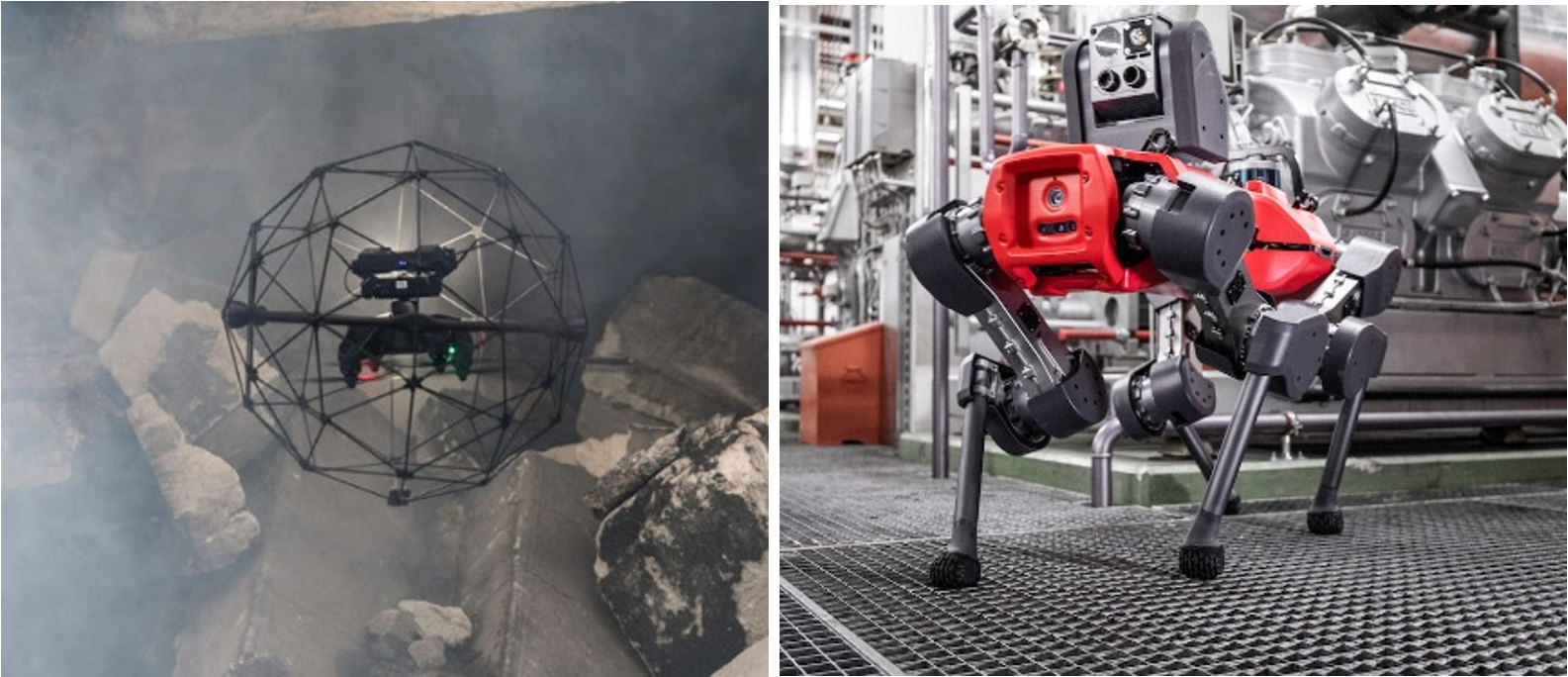
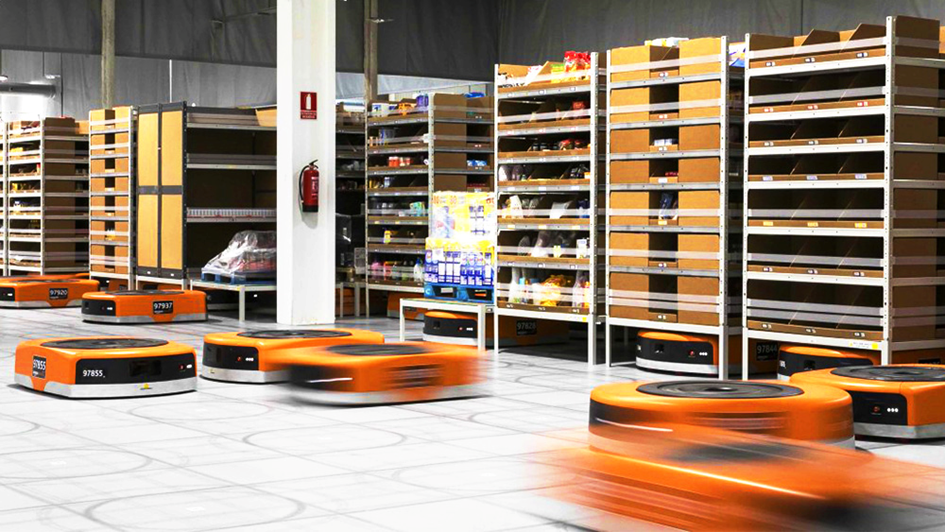
What should be considered during implementation?
A growing range of industrialized systems and components is facilitating access to mobile robotics. This is making it easier to develop more and more fields of application, which in turn promotes standardization and expansion of the commercial range of solutions.
Ultimately, development in recent years has made it possible to implement many applications in industry, logistics, and services with reasonable effort and risk despite high system complexity.
So what does the Helbling Mobile Robot teach us?
As with other system projects, the key to success is first of all precise knowledge of the requirements of the target application. The system architecture is designed and suitable system components are evaluated on the basis of this. During implementation, the focus is on technological or process risks, which must be understood and eliminated at an early stage and in rapid iterative cycles.
To demonstrate this, Helbling designed a showcase in which the essential elements of autonomous navigation were implemented in a typical application using commercially available components and software modules.
The result is a platform for autonomously detecting and manipulating objects – affectionately called HelMoRo (Helbling Mobile Robot) by its developers. HelMoRo captures the environment and autonomously builds up a digital map of its surroundings. Using the data from its optical camera, HelMoRo is also able to distinguish and categorize objects. HelMoRo is 3d-printed in an attractive and changeable design.
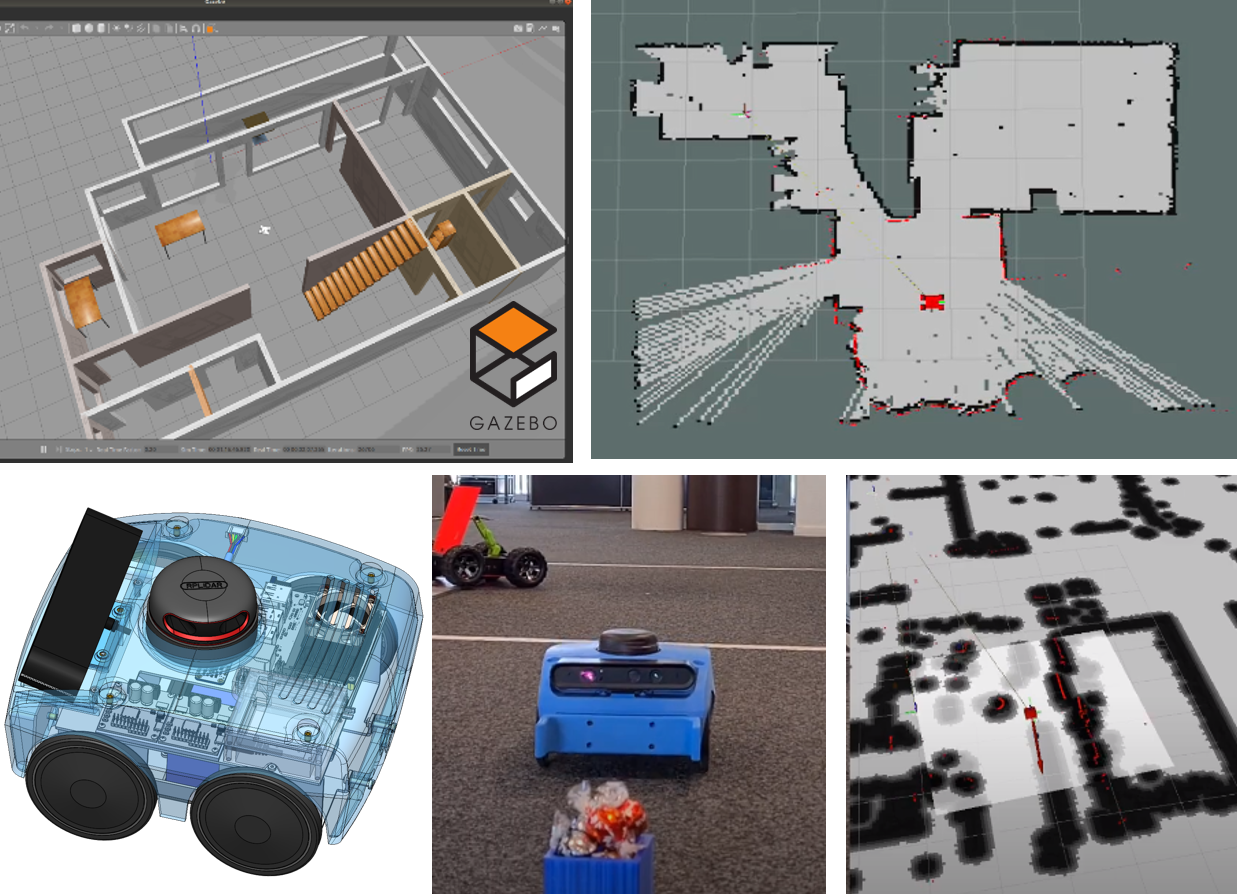
HelMoRo was developed using agile methods. After defining the target application and creating the system concept, the key components for navigation were selected. The algorithms for object recognition, mapping, localization, and path planning were developed, tested and optimized with first loops in a virtual environment (digital twin). To continuously convert findings into physical implementation, the team used rapid prototyping methods, which enabled fast verification of simulation results and a high development speed.
Summary: Helbling demonstrates the use of autonomous navigation with reasonable effort and risk
In HelMoRo a demonstrator has been created with relatively little effort. Its development spans Helbling’s entire range of expertise: from system architecture to sensor technology and algorithms, from mechatronics to industrial design. The example demonstrates how an experienced team is able to efficiently create complex individual robotics solutions using commercial components.
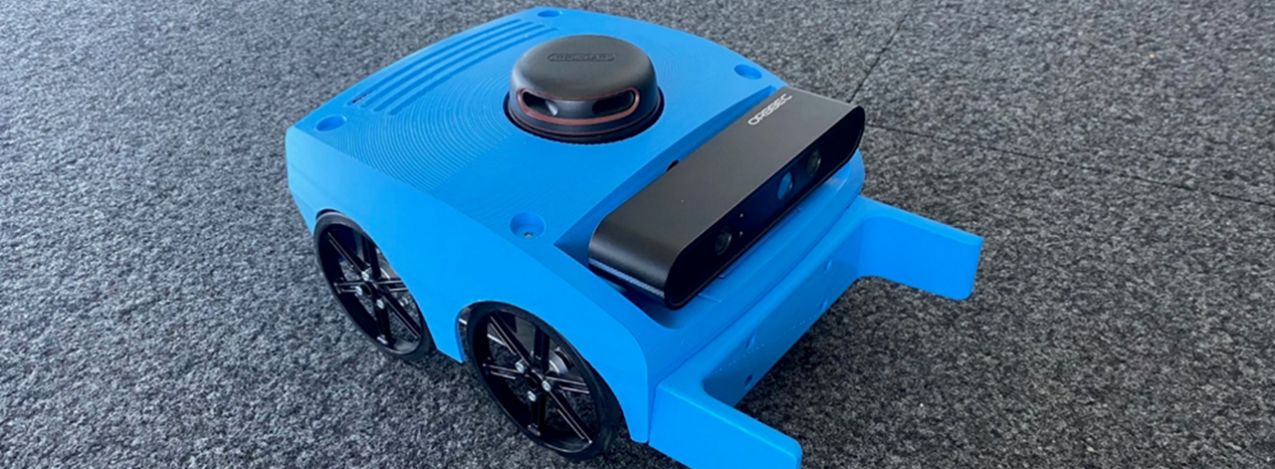
Author: Beat Zumbühl