July 2023
Dynamic material flow simulation has proven to be a powerful tool for mastering complex production and logistics systems in a dynamic industrial environment. It can be used to prove the feasibility of concepts, validate the design of systems, and test scenarios or expansion stages. However, implementing a simulation model is also associated with efforts and costs. Just like other software tools, dynamic material flow simulation can be a powerful tool when used correctly or it can generate a lot of effort without providing much benefit if it is applied in the wrong context. Therefore, whether the benefits of a simulation outweigh the costs of implementation depends on a simulation expert’s experience. Having been faced with this challenge on a regular basis in various projects, Helbling has developed a generic simulation framework to create as much value as possible from dynamic material flow simulation.
Main drivers for the use of dynamic simulation models
In projects for factory planning or process optimization, there are usually two main drivers triggering the necessity of dynamic simulation models. One is to master the complexity level of systems with a large number of dynamically interacting elements that can no longer be mastered with static calculations. In this context, a dynamic material flow simulation can be compared to a navigation system in a car, which is not of great benefit in a small village where everything is familiar but can be a very helpful tool in unknown big cities. The other driver is the mitigation of risks in projects, which are usually associated with high costs caused by errors in implementation and operation.
But the more complex and/or risky a project is, the more detailed the required granularity that usually needs to be considered in a simulation model to represent the relevant influencing factors of a system with adequate accuracy, and hence the higher the efforts and costs of implementation. Therefore, many companies are faced with the dilemma that the greater the need for simulation and the greater the benefits it could provide, the more effort is required to implement an adequate simulation model capable of adding value to the project.
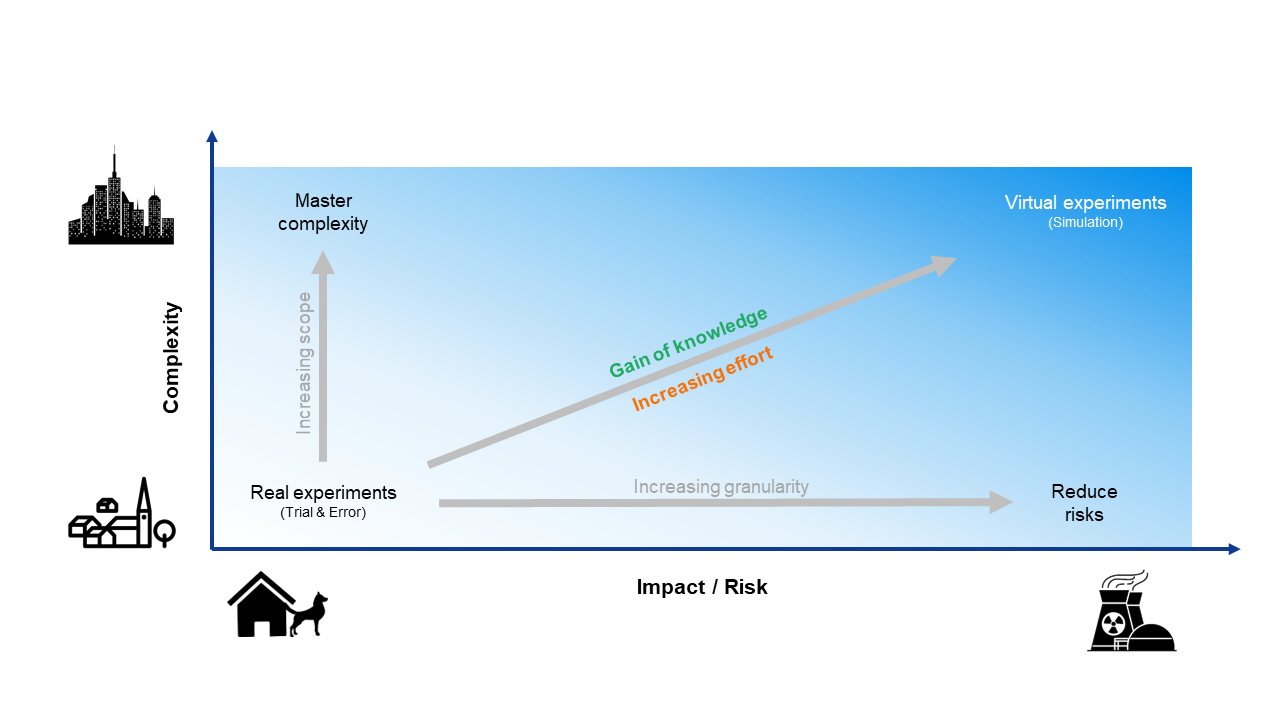
How to reduce effort in setting up a simulation
In order to reduce the effort of implementation and thus to lower the hurdle for using simulation, especially where it is needed most, this dilemma can usually be resolved through standardization. In a more or less stable environment, this can be realized rather easily by building a customized library with pre-configured simulation modules. However, this becomes very difficult when using simulation in constantly changing environments across different projects and industries. So how can simulation be standardized without compromising flexibility?
Standardizing simulation models without compromising flexibility
If the specific functionalities of a library object itself cannot be harmonized, all the attributes and interfaces defining the context of an object in the respective simulation model can be standardized. This allows each object in a simulation model, regardless of its specific functionality, to be defined by its generic properties, from the module's location and orientation to its connection to other objects and its interfaces to production planning or analysis tools. This way, the specific objects of a library themselves can be customized according to the project requirements, while everything else defining the position and interaction of an object in a model can be standardized as long as the interfaces of each library object are compatible with the generic simulation framework.
Such a standardized simulation environment allows for expression of a simulation model as an abstract set of numerical data (master data) or, vice versa, a set of numerical data can be used to create a simulation model. Hence, instead of creating simulation models themselves, Helbling has developed a generic simulation framework based on commercial simulation software capable of configuring various sites and scenarios within the same generic simulation framework without compromising the benefits of customized libraries. Thinking of simulation no longer in terms of simulation models but rather as different configurations of a generic simulation framework, the model itself is just a combination of different standardized library objects created by an algorithm according to the defined master data.
Since all interfaces of the individual modules are standardized, the simulation model can be executed by a central set of algorithms and evaluated with a central evaluation toolbox. The simulation model as well as the results can be exported for further processing. The generic simulation framework can be applied to various fields of application in the general cargo manufacturing industry and has successfully been applied in various industries.
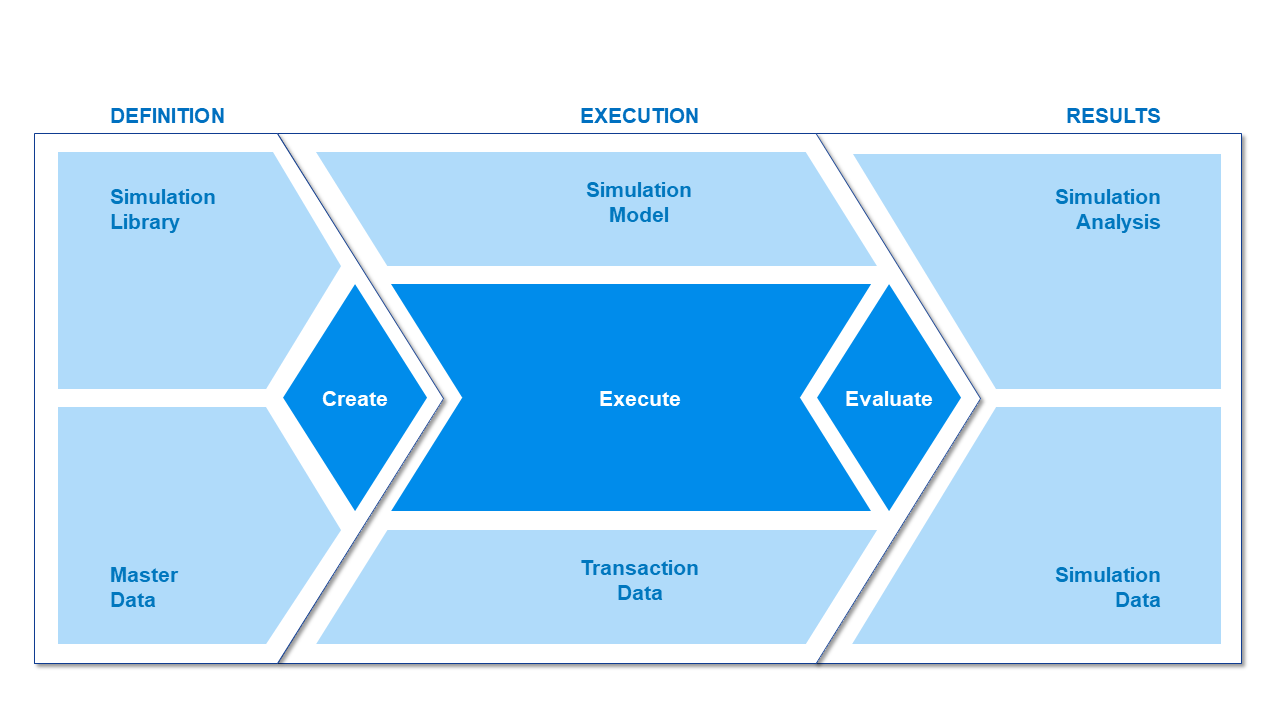
1. Model definition: Creating various simulation models within a generic simulation framework
Taking a closer look at the master data defining a model in a generic simulation framework, it contains information such as:
- Position and orientation of each object
- Intralogistics connections and types (e.g., conveyors, shuttles, AGVs, FTEs, lifts, etc.)
- Building information and graphics
- Product portfolio, including bill of material for each product
- Process parameters (e.g., cycle time, OEE, etc.)
- Control parameters (e.g., planning parameters, shift calendars, etc.)
A scenario defined by a set of master data can be imported into the generic simulation framework to combine the standardized library modules to create a simulation model automatically via an algorithm. Vice versa, a manually created simulation model within the generic simulation framework can be saved and exported as a new set of master data. In this way, an unlimited number of different sites and scenarios can be created, managed, and evaluated within the same standardized simulation environment. In addition to layout and product information, 3D architectural models can also be integrated into the master data to create true-to-scale simulation models embedded in their architectural environment.
2. Model execution: How to manage constantly changing environments
Once the simulation model has been created, all library modules within the model will be controlled by a central set of generic algorithms coordinating the different activities such as production planning, capacity allocation, etc. All relevant information will be copied from the master data to the transaction data to update and control the relevant information of the simulation run via the standardized communication interfaces.
But how can a constantly changing network with various types of intralogistics technologies such as conveyors, shuttles, FTEs, AGVs, or lifts be navigated? As all layout information is available in the master data, the network can be calculated according to the principles of the "shortest path problem" from the graph theory. As in modern navigation systems, movable units can navigate through the system by calculating the shortest path for each point in the model based on Dijkstra’s algorithm. If the type of intralogistics technology does not change, standard approaches can be used for navigation (automatic routing). But this becomes more difficult if the shortest path consists of different types of intralogistics technologies. Hence, whenever the type of technology on the shortest path changes, the algorithm defines the respective interface as an intermediate target.
3. Model results: Evaluation and monitoring of relevant information
During and after a simulation run all relevant data is available in the transaction data for detailed evaluations. As each module is tracking its own activities, all information can be monitored via standardized communication interfaces in a central evaluation panel with different analysis tools. Of course, the data can also be exported for further processing with Excel, Python, or other tools.
Summary: Generic simulation framework minimizes risks and reduces costs
A generic simulation framework allows the creation of a great variety of scenarios or expansion stages based on standardized communication interfaces without compromising flexibility. By introducing a generic simulation framework, Helbling can support customers in significantly reducing the effort and cost of implementing new simulation models and libraries, while quality can be improved through pre-configured and pre-validated interfaces. A generic simulation framework relieves the developer of unproductive programming activities by focusing on the truly value-adding features of a dynamic material flow simulation.
Author: Wolfgang Yorck
Main Image: Midjourney