
Artificial Intelligence is one of the defining technological trends of this decade. In particular, vision-based AI applications, where camera data is processed directly on the edge, are gaining rapid momentum. Embedded Vision systems are the backbone of these solutions: they enable high-performance, energy-efficient image processing directly within the device, without cloud dependency and with minimal latency. At Helbling, we rely on customized Single-Board Computers (SBCs) that significantly outperform standard solutions in terms of cost, performance, and integration to achieve this. Recent projects in smart farming, industrial automation, and security & defense clearly demonstrate the potential: System complexity for the customer is reduced, manufacturing costs are lowered, and scalable solutions for series production are created. Overall, Helbling's modular reference design for embedded vision systems minimizes development effort and project risks.
Embedded vision systems are intelligent systems that enable computer vision technologies to be integrated into a single device. They typically consist of an image sensor with a lens—such as a camera or camera module—a processing unit like a processor or microcontroller, and dedicated software for image processing and analysis. These systems capture and analyze visual data in near real-time, allowing autonomous decision-making based on visual input. Applications span a wide range of industries, including automotive, industrial automation, medical technology, autonomous robotics, and smart buildings (see also: Factbox).
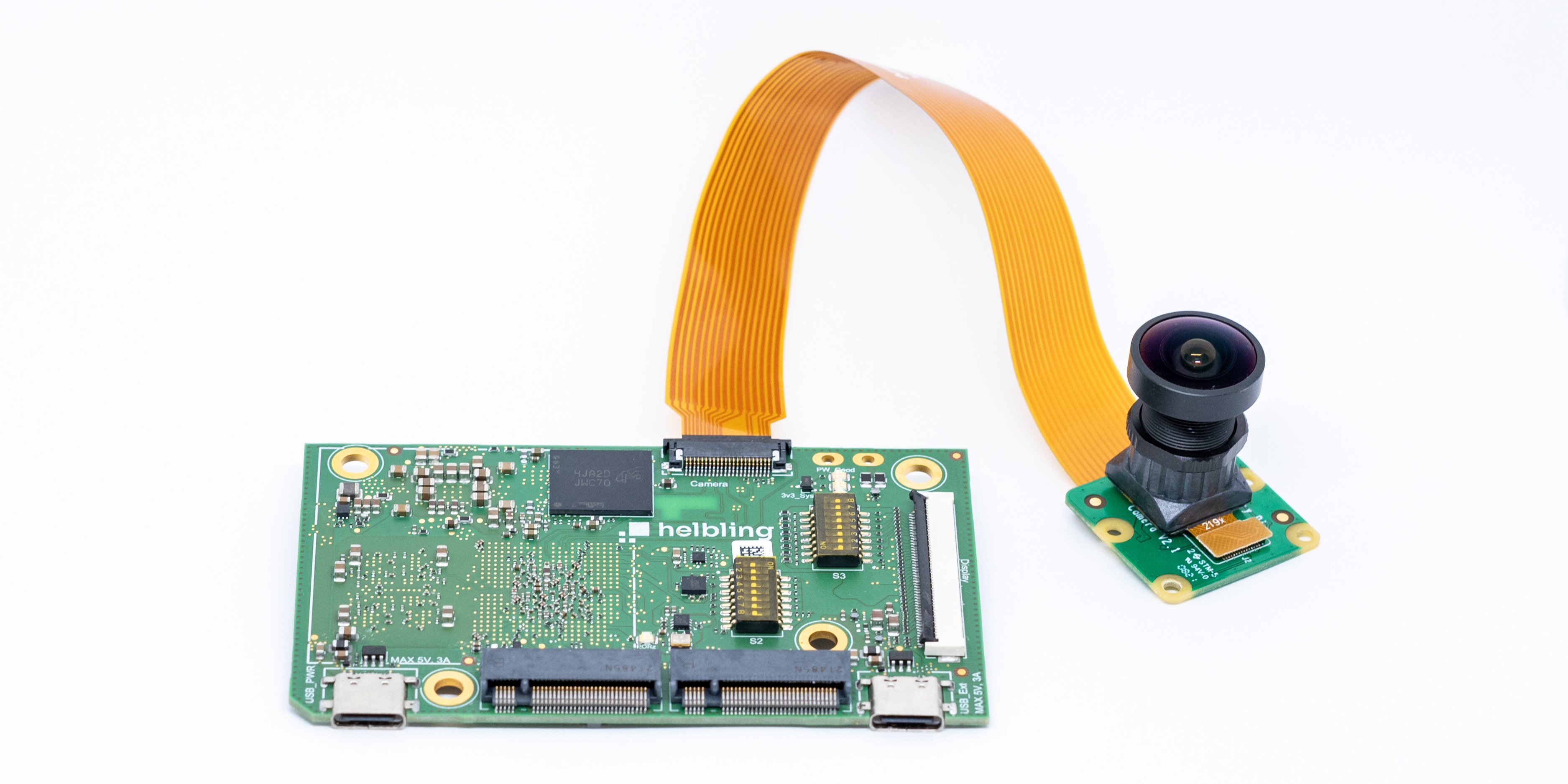
Over the past few years, Helbling has successfully implemented numerous projects in these areas and developed a modular reference design that offers substantial advantages in terms of development time and manufacturing costs.
Are there any hidden costs?
To fully exploit the advantages of integrated image processing systems, especially in series production, customized, highly integrated system solutions are required. Standard single-board computers (SBCs) are often oversized and therefore unnecessarily expensive. In combination with low-cost camera modules, manufacturing costs can be significantly reduced. Practical experience shows that direct sourcing of a camera from a Chinese manufacturer can reduce costs by a factor of 8 to 10 compared to systems from European distributors. This is not uncommon for only the camera with a lens – provided that the requirements are precisely analyzed and the customer is open to optimizing their supply chain.
However, cameras are not the only cost drivers. Conventional SBCs or system-on-modules (SoMs), such as those based on the NXP i.MX8, can also increase costs – often without delivering real added value for the embedded vision application. Here, the system can be significantly optimized with a slim and tailored selection. Moreover, when you use a SoM, every additional partner in the supply chain increases the overall cost of the system. When using SoMs, both the SoM manufacturer and the electronics manufacturing service (EMS) provider take a margin.
The solution: tailored SBCs
A tailored SBC can be designed precisely to the specific application. All components required for the product can be integrated directly on-board. The dimensions are chosen freely, which allows for seamless product integration. The result is a system that contains only the functions and components that are actually needed and does exactly what it is supposed to do – without any unnecessary additional components.
In addition to the technical design, the choice of processors plays a key role. As an alternative to traditional solutions, there are attractive options available from established manufacturers such as TI, ST, and Rockchip, as well as from new companies such as Ambarella and Hailo. These suppliers offer processors that are optimized for vision applications, thus providing powerful and cost-effective options.
The elimination of external modules, licenses, and unnecessary interfaces results in an optimized supply chain with reduced complexity, which is ideal for cost-sensitive applications. All of these advantages can be optimally exploited with a tailored SBC.
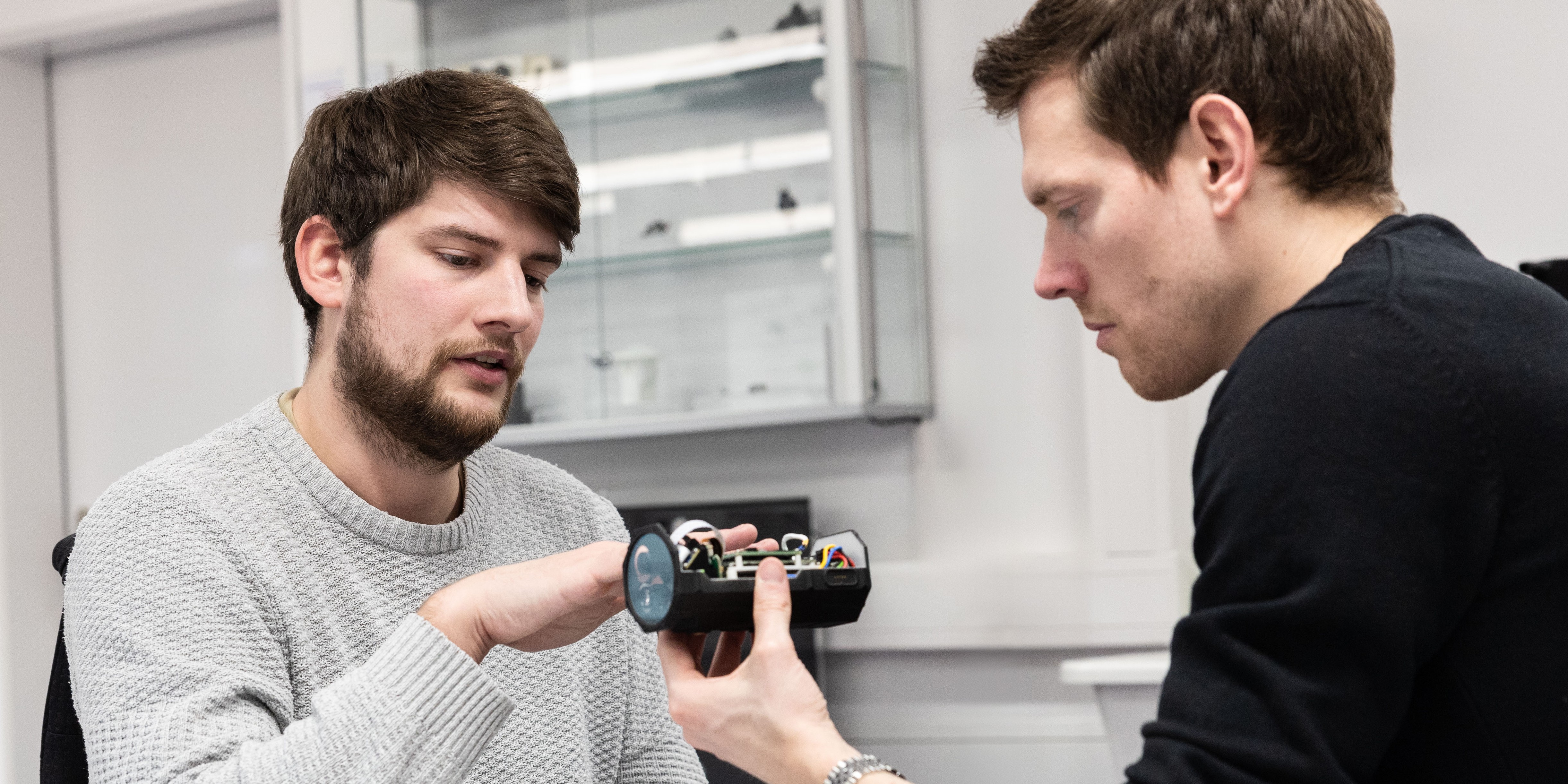
Modular instead of black box: Helbling's modular reference design for tailored SBCs
Developing a tailored SBC usually involves a great deal of effort, with long development times, considerable costs, and high technical risks. This is exactly where Helbling comes in with its modular reference design. It is based on a modular principle and serves as the basis for the development of specific SBCs.
This reference design has been implemented as a prototype and extensively tested. Thanks to the modular principle, it can be tailored to individual customer requirements in terms like performance, interfaces, form factor or costs. The advantages lie in lower development costs, shorter time-to-market, and calculable risks.
An example: potential cost savings through targeted interface choice
A key component of Helbling’s expertise in the modular adaptation of reference designs is the targeted choice and modification of components, especially in terms of performance and interfaces. This is where manufacturing costs can be reduced, while at the same time creating functional benefits. A practical example is the camera interface: USB is marketed by many camera manufacturers as the plug-and-play standard solution. There is significant potential for optimization right here. The MIPI interface (Mobile Industry Processor Interface) offers numerous technical and economic advantages:
- No unnecessary signal conversion: Almost all image sensors have a MIPI interface. By connecting this interface directly to the SBC, additional components for converting the raw image data from MIPI to USB signals are not required.
- Improved image quality: Most processors suitable for vision applications have an integrated ISP. The raw data continuously streamed via the MIPI interface can be optimized with the processor's ISP (image signal processor). This uses modern ISP tuning algorithms, as found in smartphone processors.
- Greater efficiency: Although tuning requires more development work at the outset, no computing power of the actual processor is wasted on improving image quality – this remains fully available for the application.
- Lower manufacturing costs: Without the conversion from MIPI to USB, unnecessary components are eliminated. This means a reduction in manufacturing costs through the targeted omission of components.
This combination of improved image quality and lower manufacturing costs generates real added value, particularly in the context of series production and is just one example of how costs can be reduced while optimizing performance.
Cost-effectiveness of a tailored SBC in practice
An example of a cost model (see Fig. 3) shows how economical this approach can be. Based on an estimated production volume of 1,000 units per year, the initial higher development costs can often be recouped within two to three years thanks to reductions in manufacturing costs achieved by using more cost-effective, customized SBC solutions. With higher quantities, this effect is achieved much earlier. Further reductions in manufacturing costs are possible through the targeted selection of cameras, optimized integration into a housing and, if necessary, illumination.
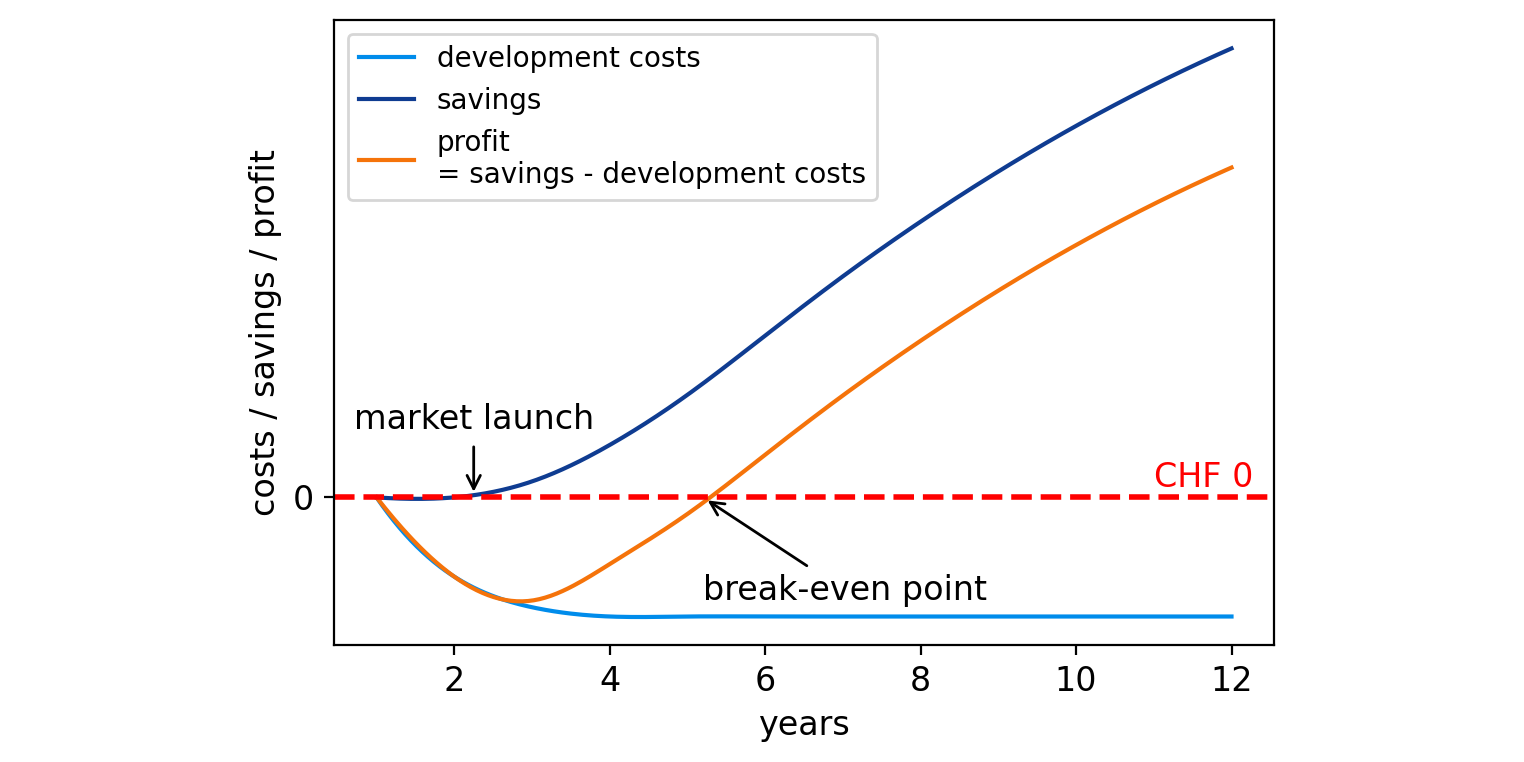
The SBCs produced in this way are extremely versatile and can be integrated into robust, sealed housings – for example, in accordance with protection class IP69 – and are vibration and shock-resistant. AI-based image processing directly on the device – completely independent of the cloud – is also possible.
Summary: Tailored SBCs as the key to reduced manufacturing costs
With increasing unit volumes, the transition to integrated, specialized solutions becomes particularly attractive. Although the original investment is higher due to the initial development costs for adapting the modular reference design with the modular principle, the economies of scale rapidly pay off thanks to a significant reduction in manufacturing costs.
With Helbling's customized SBCs, the cost-effectiveness of embedded vision systems is increased.
Authors: Sophie Jenne, Johannes Eckstein
Main Image: Helbling Technik