Technologies
July 2022
Mechanical vibrations perform many useful tasks in our daily lives. Vibrations at inaudible high frequencies are particularly convenient as they can be very powerful and specific in their effect but are not perceived as a nuisance. The technical systems that generate such vibrations are often based on piezoelectric actuators and developed specifically for each application. The technology has matured a lot since it was invented and combinations with powerful, cost-effective electronics are opening up more and more applications. Helbling has been offering customized, high-frequency vibration systems for more than 15 years and its customers can benefit from its specialized lab infrastructure and multidisciplinary competence.
The smallest vibrations with a big effect
After a long day at work, Peter returns home and slowly drives his car into the garage. The parking assist system beeps with increasing intensity as the bumper gets closer to the wall. Peter lets the car roll until the beeping reaches the familiar, continuous note. He trusts the system and does not need to worry about scratches to the bodywork.
He does not hear that the parking assist system also emits other sounds during this time. The system uses sensors in the bumper that continuously let off short ultrasound (US) beeps and measure the time until the beep bounces back from the wall. have been engineered to generate vibrations at such a high frequency that Peter cannot hear them, but they are strong enough that the echo can reliably be detected.
The resonant piezo actuators that generate vibrations were invented over half a century ago for submarine sonar. Today, they are involved in many other uses besides finding submarines and parking cars. They can measure flow in oil pipelines, weld plastic in industrial assembly lines, clean parts in a workshop, descale teeth at the dentist (fig. 1), thoroughly mix chemicals in a lab, focus cameras, or observe a fetus in the mother’s womb.
Helbling has developed piezo actuators for its customers over a broad range of applications: hearing aids, surgical tools for breaking hard materials, diagnostic instruments for cell analysis, to vaporize perfumes, or to move the gears in a watch.
Engineered for vastly different uses, the actuators can be very diverse: as small as a grain of rice or as large as bottle of wine, as strong as an ant or as destructive as a power drill, working alone or in a synchronized arrangement of dozens of devices.
Nevertheless, they do have a few things in common: they generate vibrations that are too high to hear (22 kHz to many MHz) and perform useful tasks at vibration amplitudes that are too small to see (nanometer to a few micrometer). They also share the same basic building blocks: an electronic circuit generating a tailored electrical excitation signal, a piezo element that converts electrical signals into submicroscopic mechanical deformations, and a vibrating mechanical body that amplifies and transmits the vibration. To work efficiently, all three building blocks must be customized for the application and finely engineered to work in tune.
Understanding the goal
At Helbling, engineering a resonant piezo actuator starts with understanding the application. The fundamental desired effect must be clear: whether the actuator will emit acoustic signals into a fluid, slide along a surface, or have a destructive impact on a solid, for example. Similarly, the application will often define the vibration frequency, amplitude, or power to be delivered with the vibration. External constraints such as lifetime, temperature, size, fabrication methods, or cost need to be understood too as they limit the choice of actuator architectures.
Understanding the parts
A resonant piezo actuator has at least two, but usually three or more, oscillators that are tightly connected in a chain, all moving to the same beat (fig. 2). The piezo element, which gives the actuator its name, contains the two crucial oscillators. One swings in the electrical world while the other swings in the mechanical world, i.e., in currents and voltages and in movements and forces, respectively. Due to the nature of piezoelectric materials, these two oscillators are very strongly coupled, like dancing twins joined at the hip. The nature of piezoelectric materials also means that high voltages (often dozens to hundreds of Volts) at the electrical twin are needed to create irresistibly forceful but tiny movements (typically far less than a micrometer).
A third, entirely mechanical, elastic oscillator may then be joined to the mechanical side to convert the tiny forceful movements into deformations, which are less strong but have a usable amplitude in the order of microns. This coupling is like a strong hand moving the tip of a whip with a flick of the wrist. An electronic oscillating circuit on the other side of the piezo element (the electrical side) can be used to achieve something similar but in the opposite sense. A suitable circuit can generate the high voltages needed by the piezo element using lower voltages, which are less dangerous, , for example through a battery, and easier to control.
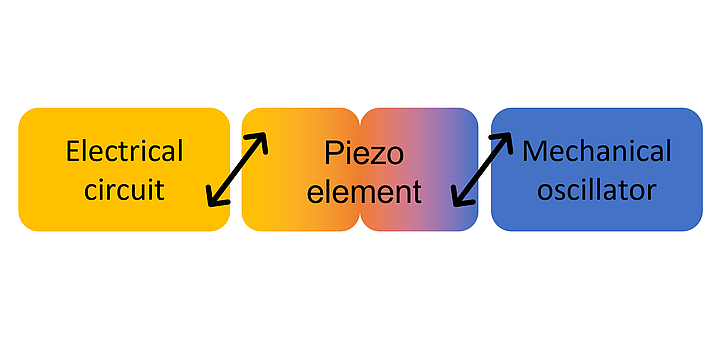
The tools for tuning
All dancers in a group must swing to the same rhythm. Anybody who has taken part in or seen a group dance knows the difference between smooth, efficient, synchronous movement and the chaos when somebody misses the beat.
All four oscillators of a resonant piezo actuator can be tuned to achieve efficient synchrony by engineering the choice of materials and dimensions. However, two aspects pose a challenge to engineers:
First, the oscillators are so strongly coupled that changing one will also affect its neighbor. Helbling relies on a solid understanding of the underlying physics combined with powerful analytical and numerical models. These can be implemented with a software tool, e.g., COMSOL Multiphysics, to design tuned systems from the start and anticipate the effects of changes (fig. 3).
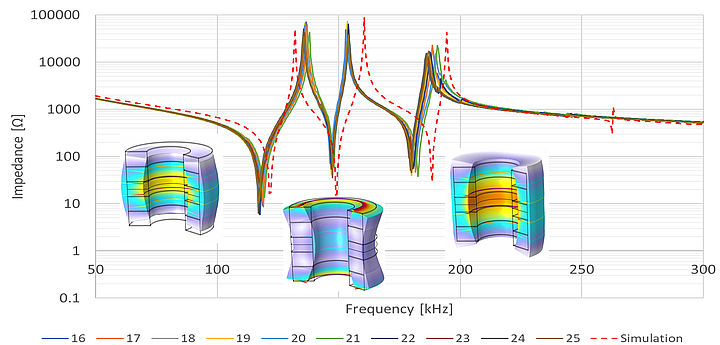
Secondly, humans are not naturally equipped to observe what is going on, neither in the electrical world nor in the mechanical world. The movements are far too small and fast. Helbling’s laser vibrometers are key here (fig.4). They allow the tiniest mechanical vibrations to be measured without even touching the vibrating system. These important instruments are complemented by fully equipped labs for developing digital and analog electronics.
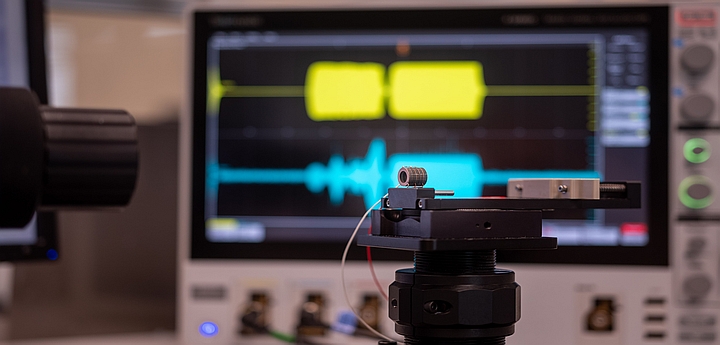
Summary: Tailored resonant piezo actuators bring unique value
Resonant piezo actuators are used in many diverse applications today. It is expected that this comparatively young technology will find it can bring unique value to the user if properly designed. Helbling has successfully offered custom piezo actuators for many years based on a broad range of competences and specialized infrastructure.
Author: Niklaus Schneeberger
Main-Image: iStock