Project
Surrogate Robotic Arm System
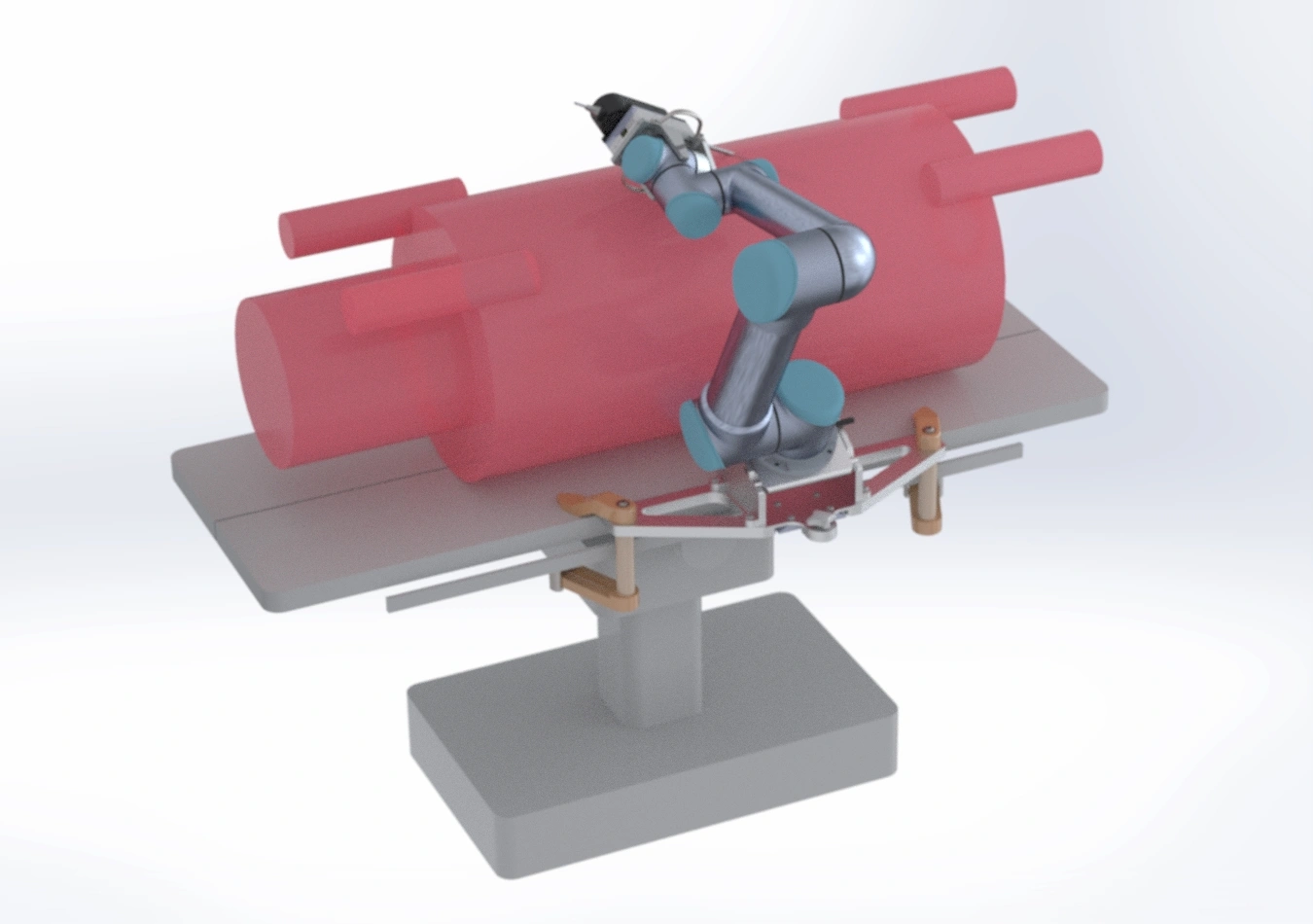
Our client is a world leader in surgical tools, engaged in developing a new suite of robotic instruments for a state-of-the-art robotic system.
We were tasked to develop and build a “surrogate” robotic arm system, which allows our client to quantify the performance of new instruments comprehensively in a pre-clinical environment. The instruments were tested with the robotic arm to evaluate their technical performance and usability preferences.
We were tasked to develop and build a “surrogate” robotic arm system, which allows our client to quantify the performance of new instruments comprehensively in a pre-clinical environment. The instruments were tested with the robotic arm to evaluate their technical performance and usability preferences.
Key Figures
- Integration of off-the-shelf (OTS) robotic arm and hand-held wireless controllers
- Lag-free real time control of surgical tool through the UI
- Iterative and closed form inverse kinematics algorithms of the tool and manipulator
- Core algorithm and GUI developed in visual C++
- Portable system, easy and quick to setup
- Integration of safety features, enabling the system to work in proximity of humans
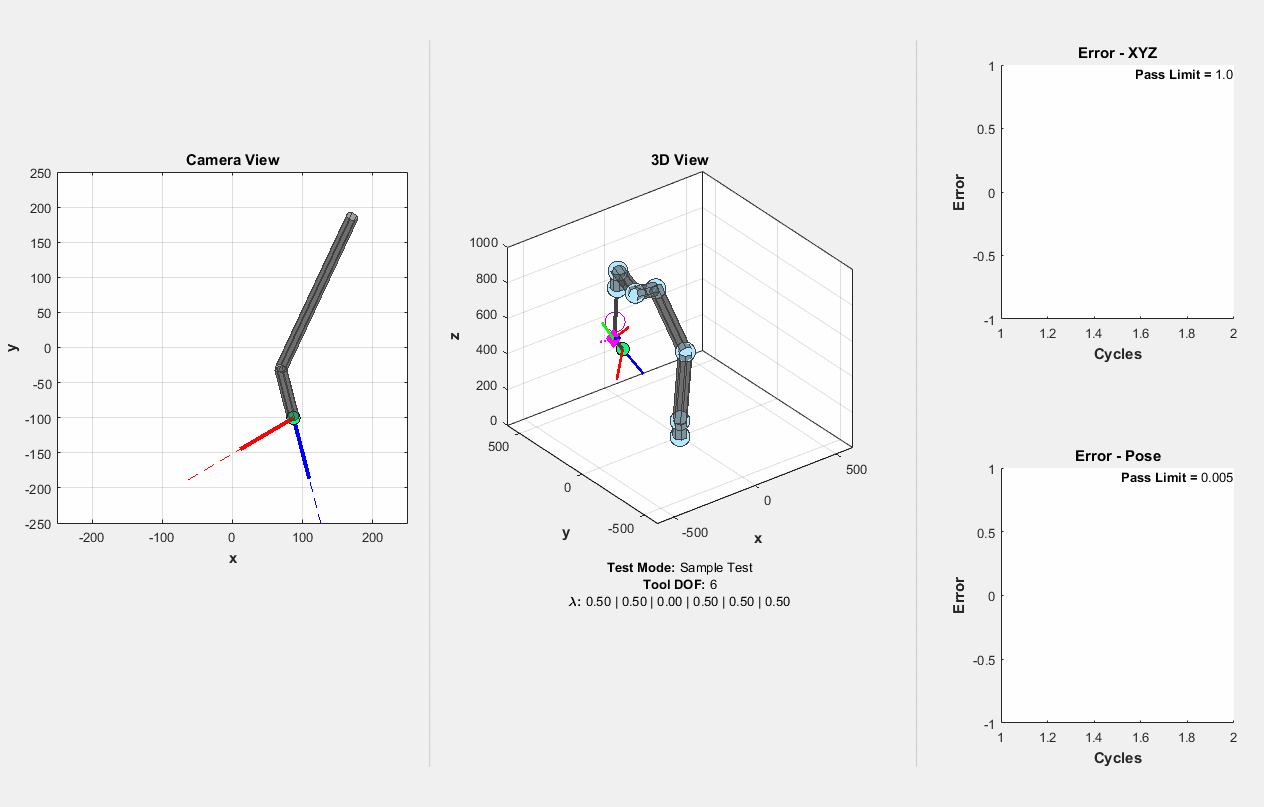
Our Contribution
- Develop a system requirements document, the overall conceptual design and the system-level layout
- Identify, select and source OTS components for robotic arm and UI
- Custom instrument tool driver electro-mechanical design
- Develop a robust inverse kinematics algorithm which maps user input to tool motion and a backlash mitigation algorithm
- Design and program a control system with a GUI
- Assembly, wiring and integration of all subsystems
- In-house functional testing and debugging of entire system
- Engineering support during in-vivo cadaver studies
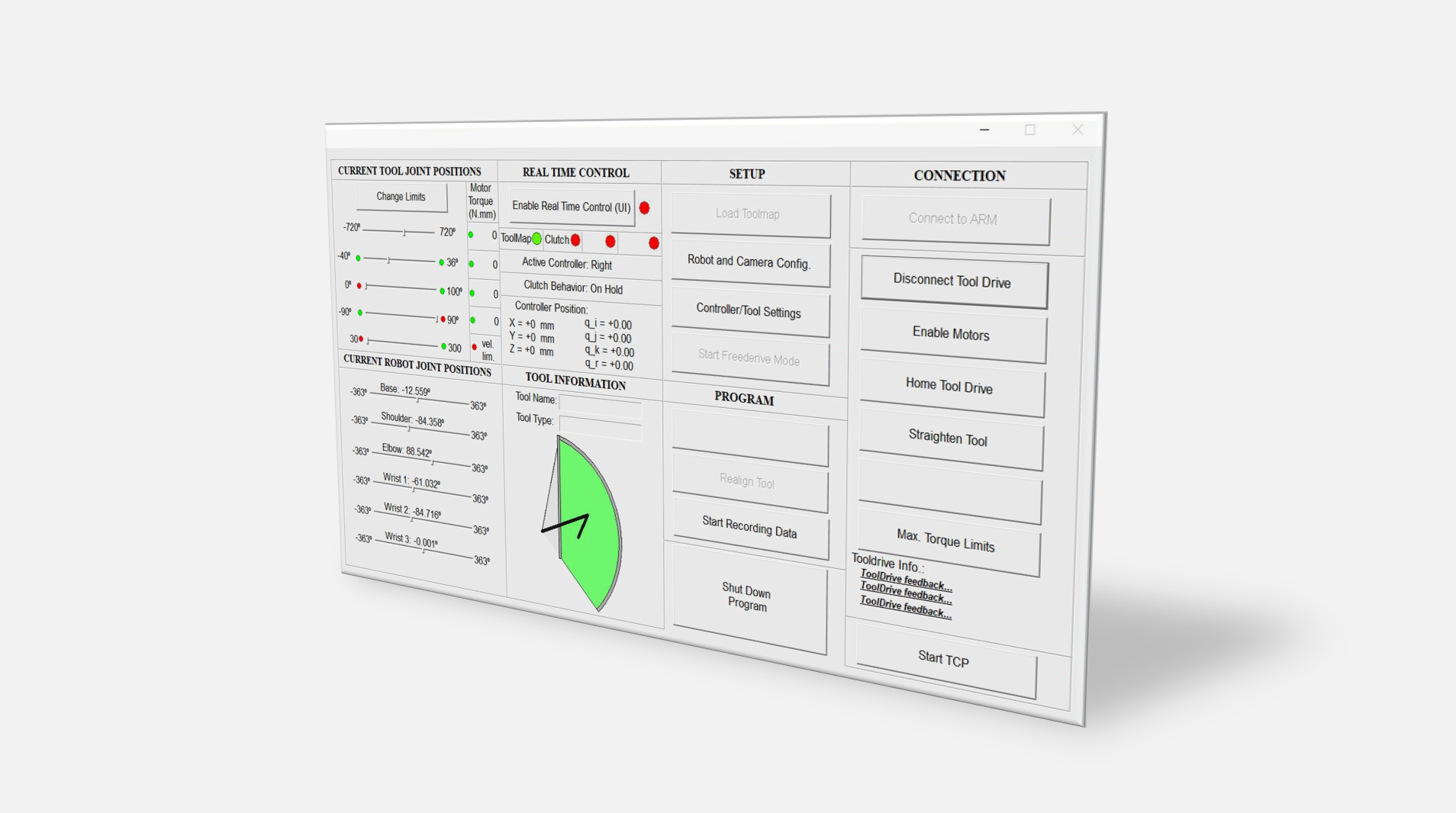
Outcome
By developing, building and testing a fully functional “surrogate” robotic arm system in record time, our customer was able to accelerate the instrument development and testing program by months.
Contact
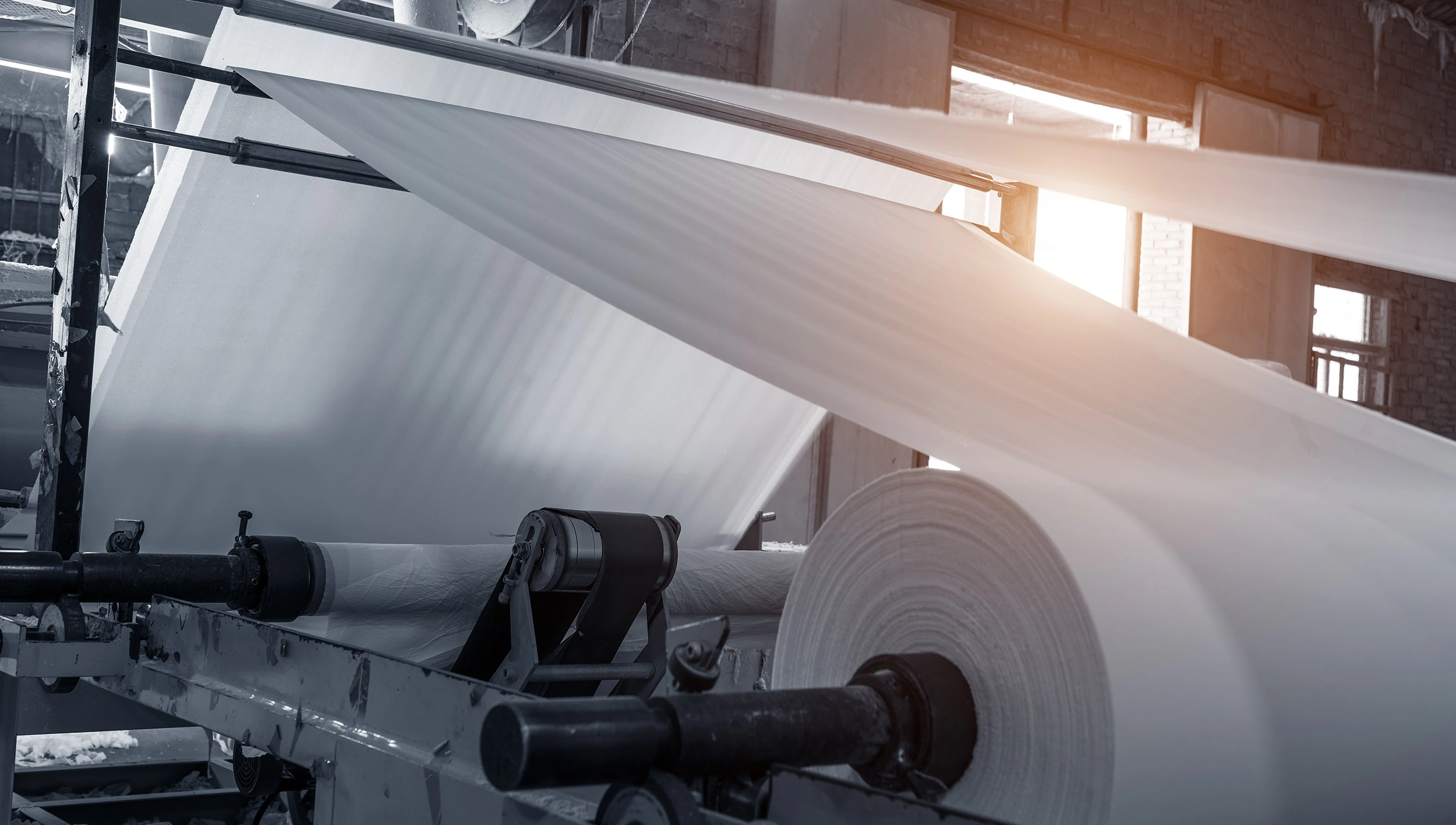
Cases
Internationales Unternehmen der Papierindustrie – Analyse des Dampfsystems
Industries:
Services:
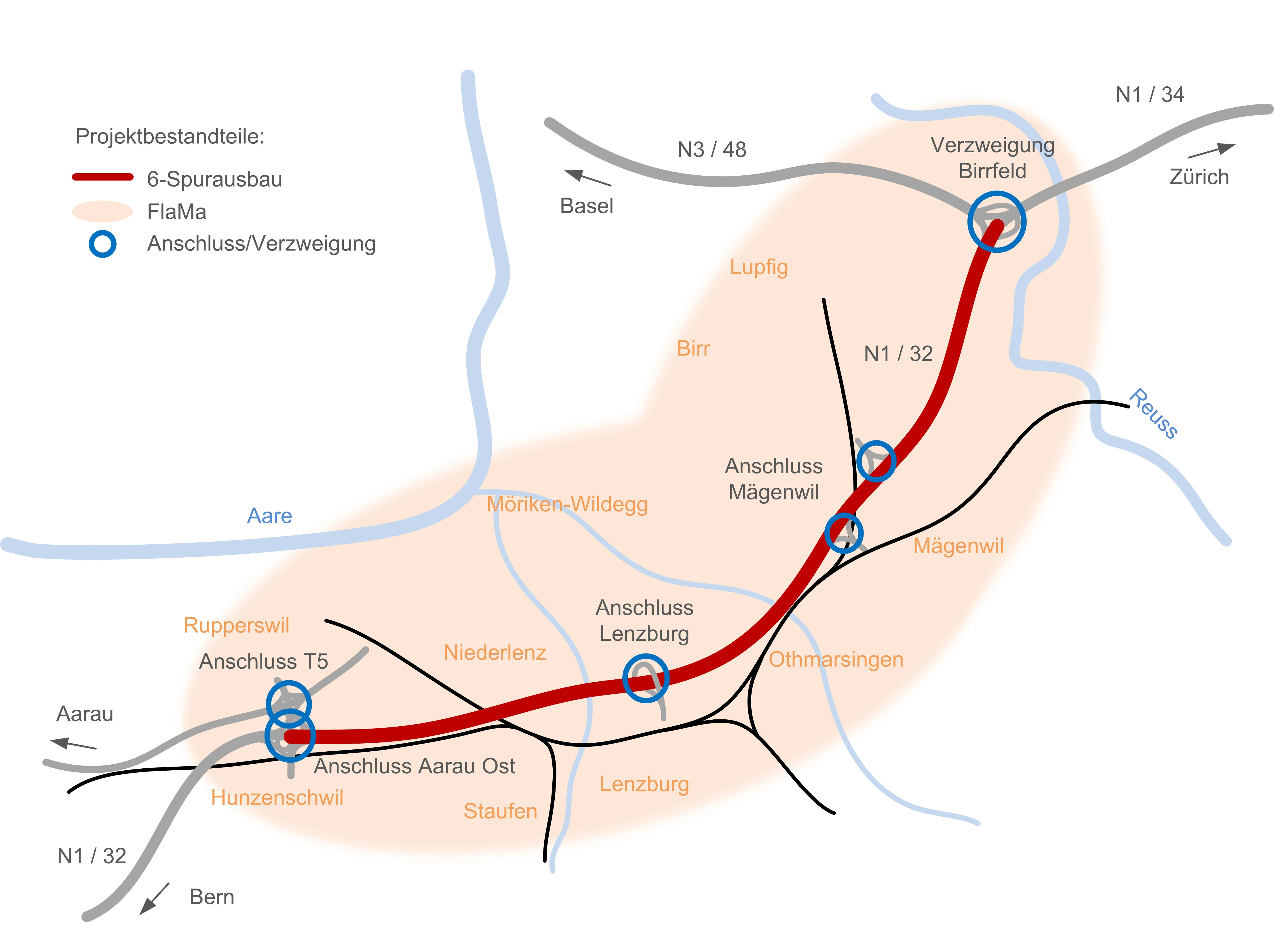
Cases
6-Streifenausbau Aarau Ost – Verzweigung Birrfeld – Bauherrenunterstützung
Industries:
Services: